The transdermal patch making and packing machine line is a highly efficient and automated system designed for the production and packaging of various types of transdermal patch products. This production line combines advanced technology and strict production standards to enhance efficiency and ensure product quality.

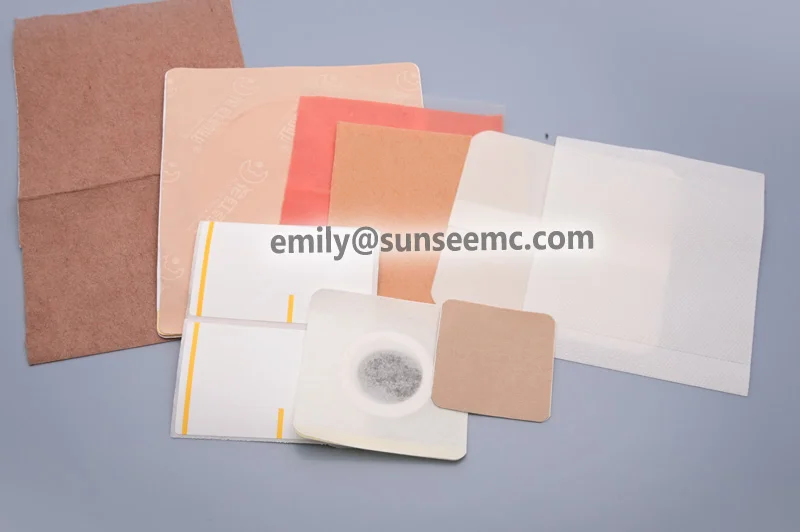
Key Features:
High-Production Efficiency: The line employs an automated control system that enables continuous, uninterrupted operation, significantly increasing production efficiency.
Precise Dosage Control: Ensures uniformity in the active ingredient content in each patch, guaranteeing consistency and therapeutic effectiveness of the products.
Multi-Functional Integration: The production line includes not just the patch-making machine but also integrates cutting, packaging, and other processes, achieving full-process automation from raw materials to finished products.
Strict Quality Monitoring: An in-built quality detection system continuously monitors the production process, ensuring each batch of products meets international standards.
Ease of Operation and Maintenance: User-friendly design and clear operational interfaces make the machine’s operation and maintenance straightforward and convenient.
Customization Service: We offer customized solutions based on different clients’ needs, catering to specific production requirements.
Application Range:
The transdermal patch making and packing machine line is suitable for manufacturing various types of transdermal drug delivery systems, including but not limited to pain relief patches, hormone replacement therapy patches, nicotine patches, etc. It is widely used in the pharmaceutical industry, biotechnology, and healthcare fields.
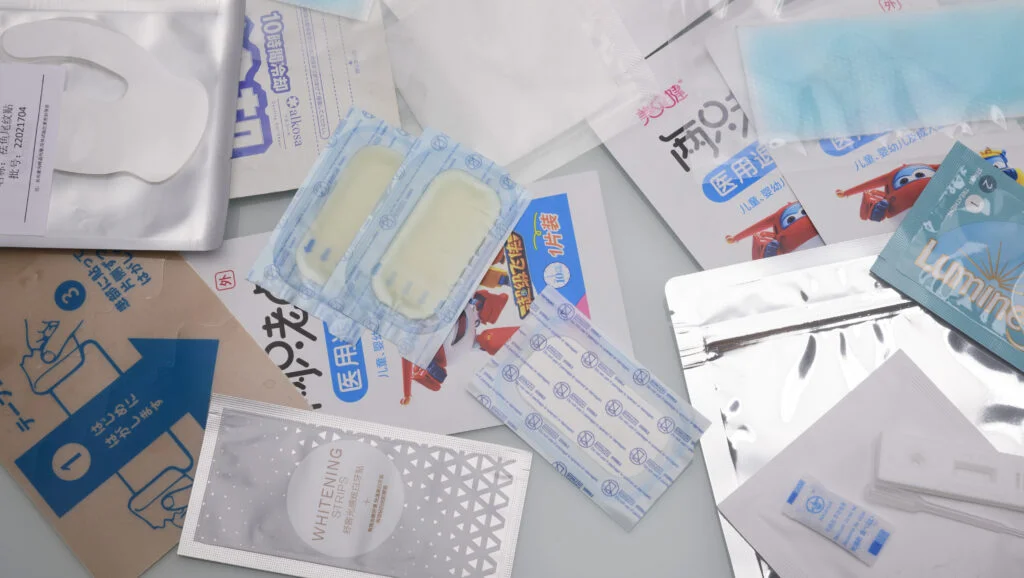
Coating Machine
The transdermal patch coating machine is a key piece of equipment specifically used in the manufacturing of transdermal patches. This machine primarily functions to evenly coat a medicinal layer on a specific substrate, playing a crucial role in producing high-quality transdermal patches.
The transdermal patch coating machine is widely used in the pharmaceutical industry for producing various types of transdermal drug delivery systems, such as pain relief patches, hormone patches, and other therapeutic patches. It is an indispensable key equipment in the pharmaceutical industry.
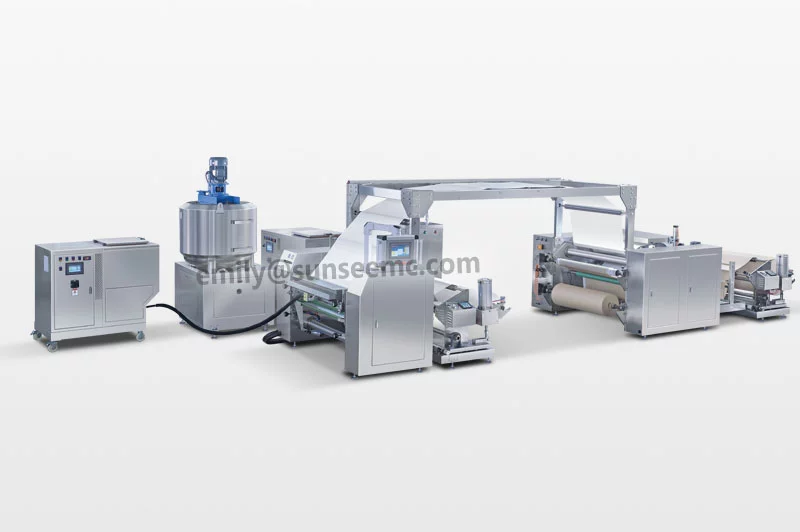
Key Features:
Precise Coating Control: The machine can precisely control the thickness and uniformity of the coating, ensuring the consistency and effectiveness of the medicinal layer.
High Production Speed: The automated operational process significantly enhances production efficiency, meeting the demands of large-scale production.
Versatile Adaptability: Capable of handling various types of substrates and medicinal formulations, it flexibly adapts to different product requirements.
Advanced Technology: Utilizes the latest coating techniques and materials to ensure the efficiency and quality of the coating process.
Ease of Operation and Maintenance: User-friendly design and intuitive control systems make it easy to operate with low maintenance costs.
Quality Monitoring System: An integrated monitoring system that continuously checks the production process to ensure product quality.
Working Process of Transdermal Patch Coating Machine
Preparation of Materials: First, prepare the raw materials for the plaster, including the drug, adhesive, and backing material.
Mixing Drug and Adhesive: Mix the drug and adhesive evenly to form the coating material for the drug layer.
Coating Process: Use a coating machine to apply the mixed drug layer uniformly onto the backing material. The thickness of the coating can be adjusted as needed.
Drying: The coated material needs to go through a drying process to remove solvents, ensuring the stability of the drug layer.
Cooling and Cutting: After drying, cool the material to an appropriate temperature, then cut it into plasters of specified sizes and shapes.
Packaging: The cut plasters are then packaged in protective packaging to maintain their stability and efficacy.
FAQ on machines
What is the working principle of a coating machine?
The coating machine is primarily used to uniformly apply a mixture of drugs and adhesives onto a backing material. It ensures the uniformity and continuity of the drug layer by precisely controlling the thickness and speed of the coating.
How to choose a coating machine based on different types of patches?
When selecting a coating machine, consider the type of patch, coating method (like knife-over-roll, roll-to-roll, or spray), the thickness of the drug layer, and production efficiency. Different coating technologies are suitable for various applications and drug release requirements.
What are the maintenance and cleaning requirements for a coating machine?
Regular maintenance and cleaning are crucial for maintaining the performance and extending the lifespan of a coating machine. Follow the manufacturer’s guidelines for routine inspections, cleaning of coating components, and replacing wear parts.
How are precision and repeatability ensured in a coating machine?
Coating machines are usually equipped with high-precision control systems and sensors to ensure accurate control of coating thickness and speed. Additionally, regular calibration and testing ensure the machine’s repeatability and reliability.
What safety features should be considered when purchasing a coating machine?
Safety features include an emergency stop button, overload protection, safety guards, and warning labels. Ensuring the machine complies with relevant safety standards and regulations is very important.
Die Cutting Machine
Die cutting machine, Or Die cutting with packing machine online. Customized on patch designs.

Packing Machine
Flow Wrap 4 side sealing packing machine for kinds of transdermal patches with auto feeder.

Box Packing Machine
Automatically filling, sealing, and labeling pre-made boxes
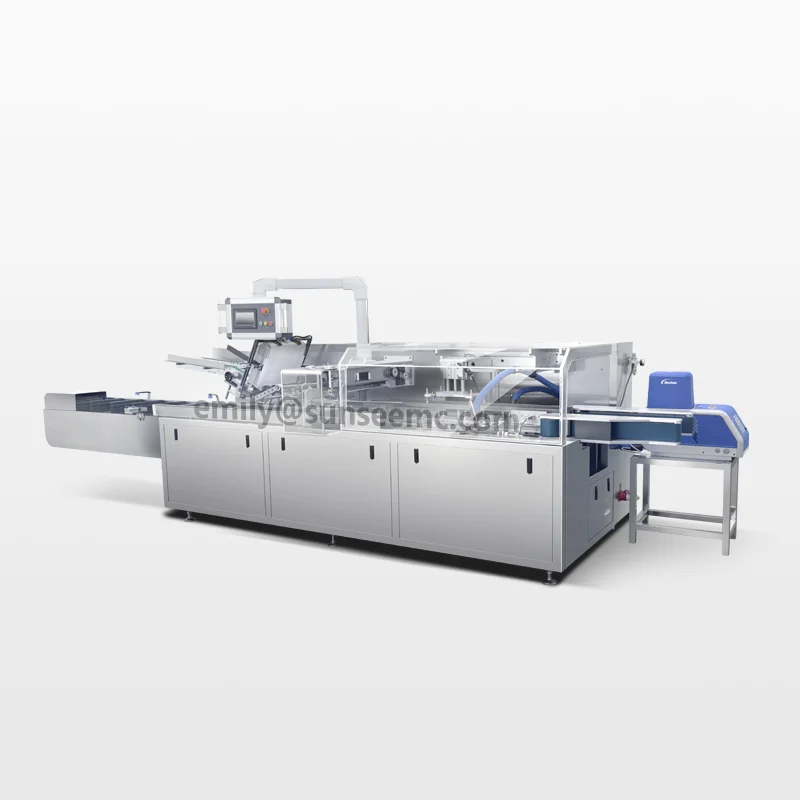
Differences in machine design for making various types of patches:
Different Coating Methods: Different patches may require different coating methods, such as knife-over-roll, roll-to-roll, or spray coating. Each method has its unique equipment design requirements.
Adjustment of Coating Thickness: Different patches may require different coating thicknesses due to variations in drug content and release rates. Therefore, the coating machine needs to be able to precisely adjust the thickness of the coating layer.
Design of the Drying System: Different types of patches might need different drying methods, like hot air drying, infrared drying, or UV drying. The design of the drying system in the coating machine should be chosen based on the characteristics of the patch.
Cutting and Shaping: Different shapes and sizes of patches might necessitate different cutting and shaping equipment. The machine design needs to accommodate these varying requirements.
Precise Control and Monitoring: To ensure the quality and consistency of the patches, the coating machine should be equipped with precise control systems and monitoring equipment.
Requirements for packing patches:
Protective Packaging: The packaging needs to protect the patches from external environmental factors such as humidity, oxygen, and light, to maintain their efficacy and stability.
Sealing Performance: The packaging material should have good sealing properties to prevent leakage or contamination of the drug components.
Anti-counterfeiting and Traceability: The packaging should include anti-counterfeiting features and information like batch numbers for tracking and ensuring product authenticity.
User-Friendly: The packaging design should be convenient for users, easy to open and use, while also ensuring safety, especially in the hands of children.
Compliance with Regulations: The packaging must comply with relevant legal and industry standards, such as pharmaceutical packaging standards and environmental regulations.
Clear Information: The packaging should clearly label product information, including instructions for use, ingredients, and expiration dates.
In summary, the design of patch packaging needs to consider product protection, user convenience, and regulatory requirements to ensure the safety and efficacy of the product.
FAQ on SUNSEE machines.
Our machinery is highly versatile and can produce a wide range of transdermal patches to meet your specific needs. Some of the common types of transdermal patches that our machinery can manufacture include:
Pain Relief Patches: These patches are designed to provide localized relief from various types of pain, such as muscle aches, joint pain, and chronic pain conditions.
Nicotine Replacement Patches: Ideal for smokers looking to quit, these patches deliver a controlled dose of nicotine to help manage withdrawal symptoms.
Hormone Replacement Patches: These patches are used for hormone therapy, delivering hormones such as estrogen or testosterone through the skin to address hormonal imbalances.
Motion Sickness Patches: Designed for travelers, these patches help prevent motion sickness by releasing medication gradually over time.
Anti-Nausea Patches: These patches are commonly used to alleviate nausea and vomiting caused by various medical conditions or treatments, like chemotherapy.
Transdermal CBD Patches: A popular choice for those seeking the benefits of CBD, these patches provide a slow and steady release of cannabidiol through the skin.
Fentanyl Patches: Prescribed for managing severe chronic pain, fentanyl patches deliver potent pain relief over an extended period.
Vitamin and Supplement Patches: These patches allow for the transdermal delivery of essential vitamins and supplements, ensuring better absorption.
Cosmetic and Skincare Patches: Beauty patches infused with ingredients like collagen, hyaluronic acid, and antioxidants for skin rejuvenation.
Our machinery’s flexibility and customization options make it suitable for producing a wide variety of transdermal patches, meeting the diverse needs of your customers and the market.
Our coating machine employs a series of advanced mechanisms and precision controls to ensure a consistent drug dosage on transdermal patches. Here’s how we achieve this:
Accurate Formulation: We start by carefully preparing the drug formulation. This involves precise measurements and quality control to guarantee the correct concentration of active pharmaceutical ingredients (APIs) and other components in the coating solution.
Uniform Coating Application: Our machine is equipped with state-of-the-art coating heads that evenly distribute the coating solution onto the patch surface. This ensures uniform coverage and consistent drug distribution across the entire patch.
Controlled Drying Process: After the coating is applied, the patches go through a controlled drying process. This step is crucial to eliminate excess moisture and ensure the drug formulation adheres uniformly to the patch substrate.
Monitoring and Feedback Systems: Our coating machine is equipped with sophisticated monitoring and feedback systems. These systems continuously analyze parameters such as coating thickness, drying temperature, and drying time. Any deviations from the set parameters trigger immediate adjustments to maintain consistency.
Quality Assurance Testing: We conduct rigorous quality assurance testing at various stages of the production process. This includes sampling and testing patches to verify that the drug dosage meets the specified requirements.
Customization Options: Depending on your specific requirements, our coating machine can be customized to accommodate different patch sizes and drug formulations. This flexibility ensures that we can meet your unique production needs while maintaining consistent drug dosage.
By combining cutting-edge technology with meticulous quality control measures, our coating machine ensures that every transdermal patch produced meets the highest standards of consistent drug dosage, providing peace of mind to both manufacturers and end-users.
Absolutely, our die cutting machinery is designed for versatility and can be easily adjusted to accommodate different patch sizes and shapes. Here’s how we ensure adaptability:
Adjustable Cutting Tools: Our die cutting machinery is equipped with adjustable cutting tools. These tools can be configured to match the precise dimensions and shapes required for your transdermal patches. Whether you need circular, square, or custom-shaped patches, our machinery can be set up accordingly.
Quick Changeover: We understand that time is of the essence in manufacturing. Our die cutting machinery is engineered for quick changeover between different patch sizes and shapes. This minimizes downtime and allows for efficient production of various patch designs.
Precision Controls: Our machinery features precision controls that enable fine-tuning of cutting parameters. This ensures that the die cutting process is accurate and consistent, regardless of the patch size or shape.
Customization Options: We offer customization options to tailor the die cutting machinery to your specific needs. If you have unique requirements for patch sizes and shapes, our team can work with you to design and implement the necessary adjustments.
Quality Assurance: To guarantee the quality of the die-cut patches, we conduct thorough quality checks during and after the cutting process. This includes inspections to ensure that the patches meet the desired size and shape specifications.
In summary, our die cutting machinery is highly adaptable and can be fine-tuned to accommodate a wide range of patch sizes and shapes. This flexibility allows us to meet your unique manufacturing requirements while maintaining precision and efficiency in the production process.
our packing machine offers both speed and efficiency, allowing you to meet production targets while maintaining the quality of your packaged transdermal patches. Its customizable settings and user-friendly interface make it a valuable asset for your manufacturing operations.
Yes, our machines are designed and manufactured to meet international pharmaceutical manufacturing standards. We prioritize compliance with stringent industry regulations to ensure the safety and quality of your pharmaceutical products.
FDA
CE
CGMP
Our machines are highly customizable to meet specific production needs. We understand that each customer may have unique requirements, and we are committed to tailoring our machinery accordingly. Here’s how we ensure customization:
Tailored Designs: Our engineering team can work closely with you to design machines that precisely match your production requirements. Whether you need specific dimensions, features, or capabilities, we can create a machine that fits your needs.
Variable Speed Control: Many of our machines offer variable speed control, allowing you to adjust the production speed to match your desired output. This flexibility is essential for optimizing production and meeting demand fluctuations.
Modular Configurations: We offer modular configurations that enable you to add or remove components to suit your production processes. This modularity simplifies upgrades and adaptations to accommodate changing needs.
Tooling and Die Options: Our die cutting machinery can be equipped with various tooling and die options. This versatility allows you to produce different patch sizes and shapes without investing in multiple machines.
Material Compatibility: We consider the materials you use in your production. Our machines can be adapted to handle a wide range of materials, ensuring compatibility with your specific product requirements.
Quality Control Integration: If quality control is a top priority, we can integrate additional quality assurance mechanisms into the machinery, such as vision systems or inspection stations, to meet your stringent standards.
User Interface Customization: The user interface of our machines can be customized to match your operational preferences. This includes user-friendly controls and interfaces tailored to your team’s needs.
Training and Documentation: We provide comprehensive training and documentation to ensure your team can effectively operate and maintain the customized machinery.
We offer comprehensive technical support and maintenance services to ensure the optimal performance and longevity of our machines. Here’s an overview of the support and services we provide:
Installation and Setup: Our team can assist with the installation and setup of our machines at your facility. We ensure that the equipment is properly positioned, calibrated, and connected for seamless operation.
Training: We provide training programs for your operators and maintenance staff. These programs cover machine operation, maintenance, troubleshooting, and safety procedures, empowering your team to use the equipment effectively.
Preventive Maintenance: Regular preventive maintenance is essential to prevent downtime and prolong machine life. We offer scheduled maintenance services to inspect, lubricate, and replace components as needed, reducing the risk of unexpected breakdowns.
Emergency Support: In the event of unexpected issues or breakdowns, our technical support team is available for immediate assistance. We offer remote troubleshooting and can dispatch field service technicians if required.
Spare Parts: We maintain an inventory of spare parts for our machines. This ensures that you have quick access to replacement components, minimizing downtime during repairs.
Calibration and Validation: We offer calibration and validation services to ensure that our machines continue to meet regulatory requirements and maintain accurate performance.
Software Updates: We provide software updates and improvements to keep your machines up to date with the latest features and optimizations.
Customization and Upgrades: If your production needs change, we can assist with machine customization and upgrades to adapt to new requirements or technologies.
Documentation: Comprehensive documentation is provided, including user manuals, maintenance guides, and technical specifications, to support your team in operating and maintaining the machinery.
Remote Monitoring: Some of our machines can be equipped with remote monitoring capabilities, allowing our technical support team to proactively identify and address potential issues.
Yes, our machinery is designed to be seamlessly integrated into existing production lines. We understand the importance of compatibility and ease of integration, and we offer the following features and options to facilitate this process:
Flexible Configurations: Our machinery can be configured to match the layout and requirements of your existing production lines. We can adapt the machine’s dimensions, placement, and interface to seamlessly fit into your workflow.
Modular Design: Many of our machines are modular, allowing you to add or remove components as needed. This modularity simplifies integration by accommodating different production setups and processes.
Conveyor Systems: We offer conveyor systems and interfaces that can be synchronized with your existing conveyors, ensuring a smooth material flow from one production stage to another.
Customized Interfaces: Our machines can be equipped with customized interfaces and control systems, making it easy to integrate them into your existing control infrastructure.
Standard Communication Protocols: Our machines support standard communication protocols such as PLC (Programmable Logic Controller) integration, making it straightforward to connect them to your existing control systems.
Compatibility with Packaging Lines: If you require packaging and labeling as part of your production, our machines can be integrated with packaging lines and labeling equipment.
Consultation and Site Assessment: Our team can conduct a site assessment to evaluate your existing production setup and recommend the best integration approach. We offer consultation services to ensure a seamless transition.
Training and Support: We provide training for your team to operate and maintain the integrated machinery effectively. This includes guidance on how to synchronize the new equipment with your existing production processes.
We prioritize energy efficiency and sustainability in the design of our machines to minimize energy consumption and reduce environmental impact. Here are the key features and initiatives we incorporate:
Energy-Efficient Components: Our machinery incorporates energy-efficient motors and components to reduce electricity consumption during operation.
Variable Speed Control: Many of our machines offer variable speed control, allowing you to optimize energy use by adjusting production speed to demand.
Resource-Efficient Design: We prioritize designs that minimize material waste and streamline production processes, promoting sustainability.
Compliance with Environmental Standards: Our machinery meets relevant eco-friendly certifications and adheres to environmental regulations and standards.
Reduced Material Waste: Our machines are designed to minimize material waste during production, contributing to cost savings and sustainability.
Ensuring the quality and reliability of our machinery over time is a top priority. We employ a combination of practices and measures to achieve this:
Quality Materials and Components: We use high-quality materials and precision-engineered components to build reliable machines.
Rigorous Quality Control: Our manufacturing process includes thorough quality checks to ensure each machine meets our stringent standards.
Regular Maintenance and Service: We offer preventive maintenance services and spare parts availability to extend machine lifespan.
User Training: Comprehensive training empowers operators and maintenance staff to care for the equipment correctly.
Technical Support: Our responsive technical support team is available for troubleshooting and timely assistance.
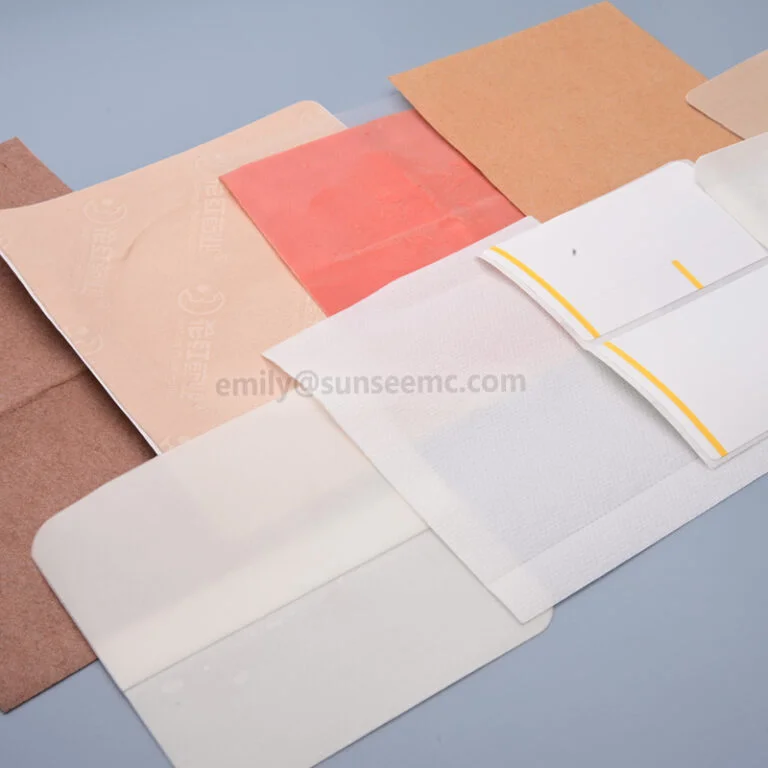