Multi-Lane 4 Side Sealing Packing Machine
A customized packing machine for transdermal patches, rapid test kits and teeth whitening strip packaging.
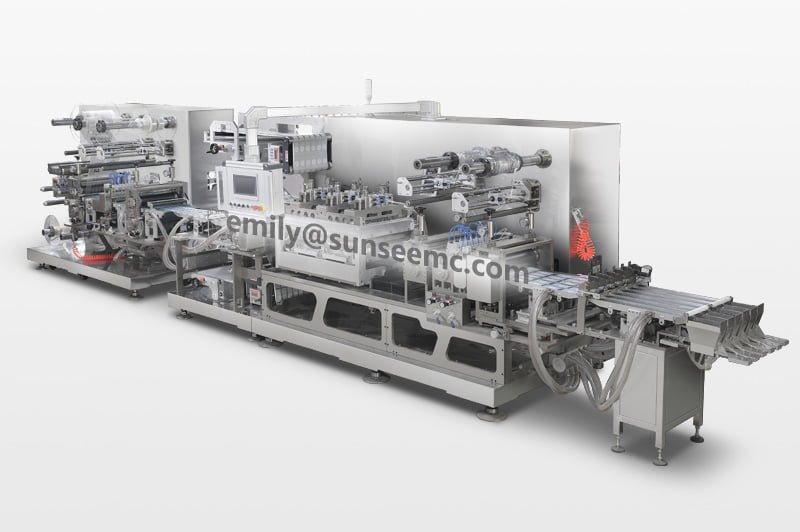
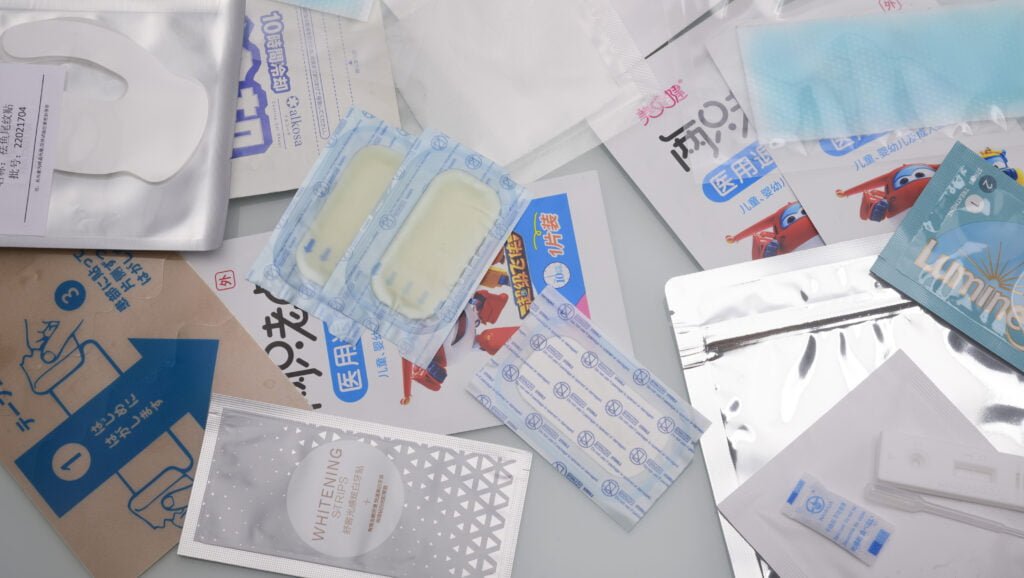
In the evolving industrial landscape, the Multi-Lane 4 Side Sealing Packing Machine stands as a robust, versatile, and efficient solution for diverse packaging needs. Tailored for businesses aiming to escalate productivity without compromising quality, this machine specializes in packaging transdermal patches, plasters, hydrogel patches, rapid test kits, teeth whitening strips, and much more.
Core Features
Multi-Lane Output
- Facilitates higher throughput by enabling packaging operations across multiple lanes, effectively multiplying output without requiring additional floor space.
Customizable Auto Feeding System
- The automated feeding mechanism ensures precision and speed, reducing manual errors and operational costs.
Four-Side Sealing Technology
- Provides secure, airtight packaging with seals on all four sides, extending product shelf-life and ensuring compliance with international safety standards.
User-Friendly Interface
- Intuitive controls simplify the setup and operation, making it easy to switch between different product types and sizes.
High-grade Material Compatibility
- Capable of handling a variety of materials, including laminates, metalized films, and paper, providing flexibility in packaging choices.
Quality Assurance Mechanisms
- Integrated sensors and quality checks to monitor seal integrity, weight, and dimensions, to ensure each package meets stringent quality criteria.
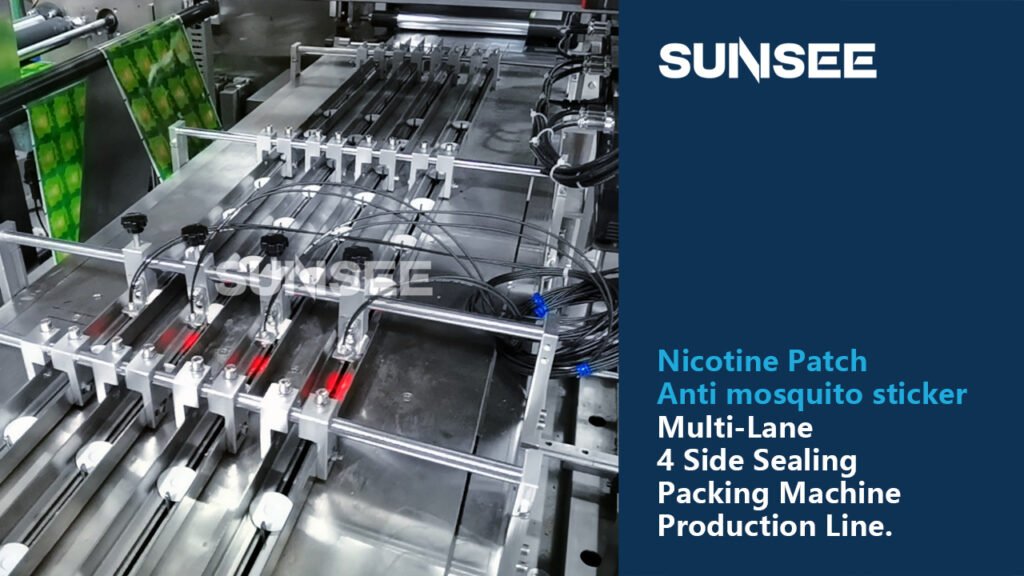
What are the advantages of a multi-lane 4-side sealing packing machine over a single-lane counterpart?
The choice between a single-lane and a multi-lane 4-side sealing packing machine primarily hinges on the production requirements and the versatility needed in packaging sizes.
A single-lane packing machine is adept at producing one package per cycle and offers significant flexibility in packaging sizes without the need to alter the mould. This makes it an excellent choice for manufacturers that require a variety of packaging sizes and have lower-volume production runs.
On the other hand, a multi-lane packing machine excels in high-volume production environments. Capable of creating between 1 to 6 packages per cycle, depending on the product size, it maximises output for a single product size. While changing to a different product size requires modifying multiple parts such as the feeding conveyor and sealing mould, the investment in time is offset by the efficiency and speed during mass production runs for a singular product size.
By opting for Sunsee’s multi-lane packing machine, manufacturers specialising in high-volume production of uniform products, such as pain relief patches or diagnostic strips, can significantly benefit from the increased production rate, thereby maximising throughput and meeting market demands promptly.
How does Sunsee's multi-lane 4-side sealing packing machine cater to the customisation needs of transdermal and pharmaceutical patch packaging?
Sunsee’s multi-lane 4-side sealing packing machine is designed to deliver not just packaging solutions but a comprehensive production line enhancement. With customisation at its core, the machine offers the following benefits:
Integrated Die Cutting: By equipping the packing machine with a die cutting feature, Sunsee enables a seamless transition from coating to cutting, streamlining the entire production process of patch manufacturing. This integration reduces the need for multiple machines and manual handling, enhancing the efficiency and speed of production.
Inline Auto Feeding System: Sunsee’s machines can be custom-fitted with an auto feeder and tailored connections to existing coating machines. This synchronisation allows for an inline production flow, significantly reducing labour requirements and minimising the risk of product handling errors, ensuring a consistent quality output.
Box Packing Integration: The capability to extend the packaging process to include box packing ensures a more automated and continuous production line. This addition minimises the transition from packaging to final boxing, readying the product for distribution faster and more efficiently.
Customisation According to Samples: Sunsee acknowledges the unique requirements of each customer by offering to tailor machines based on provided samples. This custom engineering ensures that the machinery aligns perfectly with the client’s existing product specifications, yielding a highly efficient packaging process customised for specific product dimensions and materials.
By adopting Sunsee’s customisable solutions, clients can benefit from a streamlined production process, which translates to lower operational costs, improved production speed, and enhanced product quality – a formidable combination for businesses aiming to lead in the competitive pharmaceutical and transdermal patch market.
Can Sunsee's packing machines be integrated with auto feeding systems for different types of products such as hydrogel patches and teeth whitening strips?
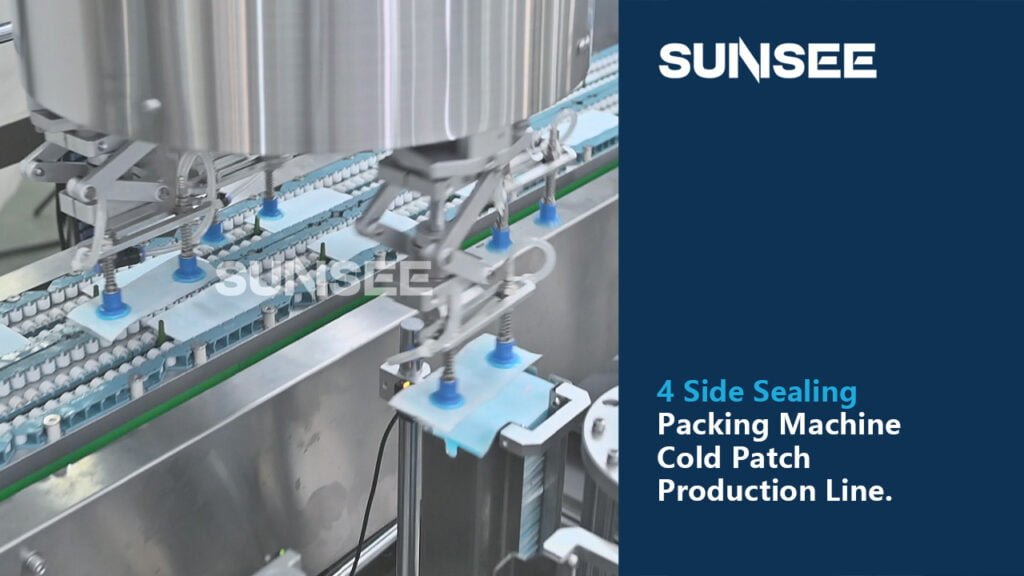
Sunsee’s packing machines are adept at accommodating a wide range of products by integrating customised auto-feeding systems. This adaptability ensures that regardless of the product size or type, from hydrogel patches to compact teeth whitening strips, the packing process remains streamlined and efficient.
For smaller products such as teeth whitening strips, Sunsee offers specially designed die-cutting equipment that works in tandem with the auto feeder, facilitating an online, end-to-end packing solution. This means that from the initial product insertion to the final sealed pack, the entire process is automated. Such an in-line system significantly reduces manual labour, minimises potential human error, and increases the consistency of the finished product.
Incorporating a customised auto feeder not only enhances efficiency but also supports scalability. As demand grows, Sunsee’s machinery can readily handle increased production volumes, ensuring that businesses can scale up their operations smoothly and meet market demands without compromising on quality or speed.
By choosing Sunsee for their packaging needs, companies can expect a bespoke, high-performing packing solution that aligns with their product requirements, driving operational excellence and supporting business growth.
Can you explain the process of plaster die cutting in packaging and its significance for product presentation?
Die cutting is a precise packaging process where a custom-shaped die is used to cut plasters into specific shapes and designs. The customisation of the die cutting mold is crucial in this process, as it allows for the creation of unique shapes that align perfectly with the brand’s design and functional requirements.
Customised Die Cutting Molds: By tailoring the die cutting mold to the exact dimensions and shape required for a specific plaster, manufacturers ensure that each product fits its packaging perfectly. This attention to detail enhances the product’s visual appeal and can help in brand differentiation, as the unique shape and packaging can make the product stand out on shelves.
Single or Double Die Cutting Options: Depending on the plaster’s design and the release liner’s complexity, a single or double die cutting mold can be used. A single die is typically utilised for simpler shapes, while a double die is beneficial for more intricate designs or when a distinct openness of the release liner is required. The choice between single or double die cutting molds directly influences the functionality and user experience of the final product. For example, a double die may allow for a ‘peel-and-stick’ feature that could offer consumers added convenience.
The significance of the die cutting process extends beyond mere aesthetics. It ensures that the final product is not only visually appealing but also functional and user-friendly. For manufacturers, this means the potential for a stronger brand presence and a better consumer experience, which can lead to increased brand loyalty and sales.
By incorporating customised die cutting into their packaging process with Sunsee’s machinery, businesses benefit from the ability to tailor their product presentation to the finest detail, providing them with a competitive edge in the marketplace.
What factors should be considered when choosing an auto feeding system for a packing machine?
Selecting the right auto feeding system for a packing machine is critical for ensuring operational efficiency and meeting production goals. Here are key factors to consider:
Consistency of the Patch: It’s essential to evaluate whether the patches to be packaged are regular in shape and size. Consistency is vital for the auto feeding system to reliably and accurately place the patches into the packaging. Irregularly shaped or inconsistently sized patches may require more sophisticated feeding systems with advanced detection and handling capabilities.
Quantity per Package: The number of pieces that need to be packed in each package also plays a critical role. The auto feeder must be capable of handling the required quantity accurately, maintaining a consistent count for each package. This ensures each package is complete and meets quality control standards.
Production Speed: The desired production speed is a crucial consideration. The auto feeding system must match the speed requirement of your production line to maintain efficiency. A system that is too slow can create bottlenecks, while one that is too fast may lead to errors or damage.
When selecting an auto feeding system, it’s important to ensure that the system can be integrated seamlessly with your current packing machinery and that it aligns with your product specifications and production demands. By taking these factors into account, manufacturers can optimise their packaging lines for higher throughput, reduced downtime, and better overall performance.
What types of products are best suited for a multi-lane 4-side sealing packing machine and why?
A multi-lane 4-side sealing packing machine is particularly well-suited for products that are typically regular in size and require high-volume production runs. Products such as teeth whitening strips, anti-mosquito and anti-drink stickers, anti-acne plasters, standard plasters, hydrogel patches, rapid test kits, and even food items like seaweed are ideal for this type of machine due to several reasons:
Regular Size: Products that have a uniform size can be packaged more efficiently as the machine can be finely tuned to accommodate their dimensions, leading to higher consistency and reliability in packaging.
Mass Production Needs: For products that have a high market demand, the ability to produce large quantities efficiently is key. A multi-lane 4-side sealing packing machine can meet substantial production requirements, ensuring that supply keeps pace with demand.
Sealing Quality: A strong and uniform seal is critical for product integrity and shelf life, especially for items that may be sensitive to environmental factors. The four-side seal provides a robust and protective packaging solution, essential for maintaining the quality and efficacy of the products.
For manufacturers, these machines offer the capability to quickly and effectively meet market demands, maintain product quality, and ensure consumer satisfaction. This results in a strong competitive advantage, as the ability to deliver products in a timely and consistent manner is highly valued in today’s fast-paced market.
What are the common maintenance requirements for a multi-lane packing machine?
Regular maintenance is crucial for the efficient operation of a multi-lane packing machine. Here are some of the common maintenance tasks required to keep the machine performing at its best:
Lubrication: Periodic oiling of moving parts is essential to reduce friction and wear, which helps in preventing breakdowns and extending the machine’s lifespan. Oiling should be done in accordance with the manufacturer’s recommendations to ensure optimal performance.
Cleaning: Given that multi-lane packing machines are often used in the food and pharmaceutical industries, maintaining hygiene is of paramount importance. Regular cleaning to remove debris and product residue ensures that the machine remains sanitary and that products are not contaminated.
Gear and Chain Inspection: It is critical to monitor the gears and chains regularly. Any signs of jumping or sticking could indicate potential issues that may disrupt the smooth operation of the machine. Addressing these early can prevent more significant problems down the line.
Belt Assessment: After 2-3 years of operation, it is advisable to check the condition of conveyor belts. Belts can wear out or lose tension over time, which can affect the efficiency and accuracy of the auto feeding system.
Adhering to these maintenance requirements not only ensures that the machine operates in a hygienic manner, suitable for its intended use in sensitive production environments but also minimises downtime and maintains the production line’s effectiveness.
Playlist
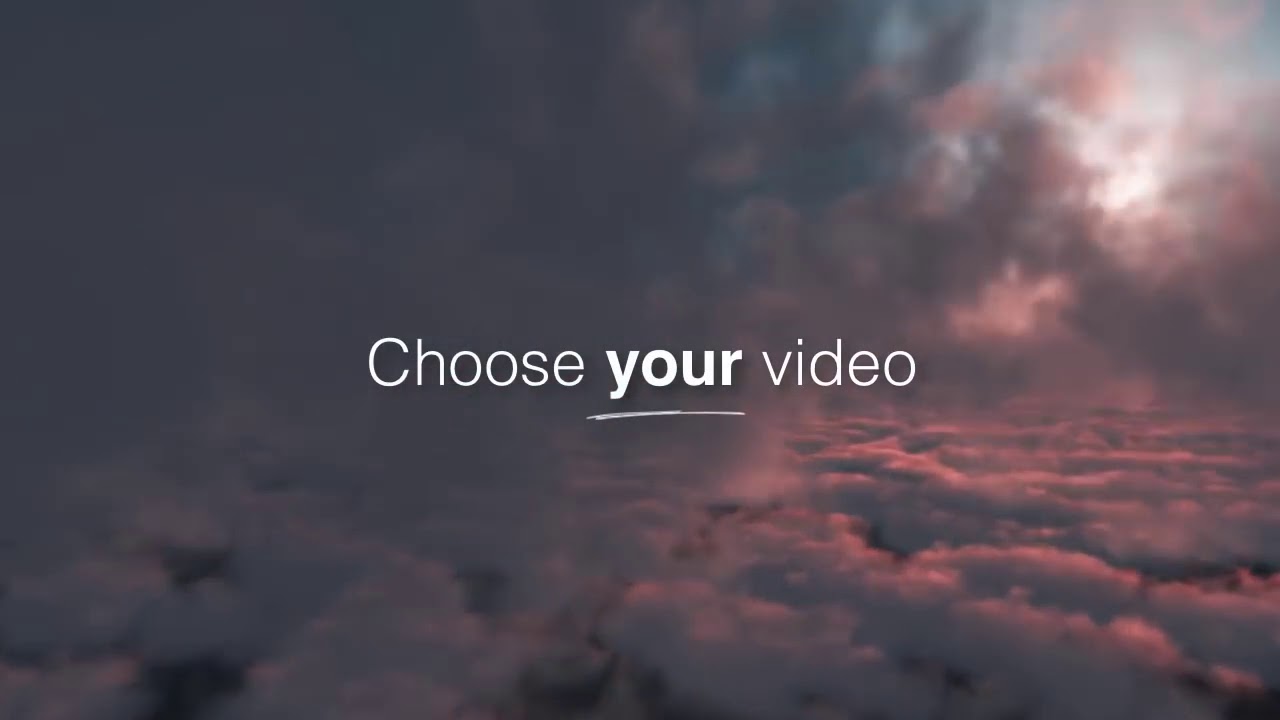
0:16
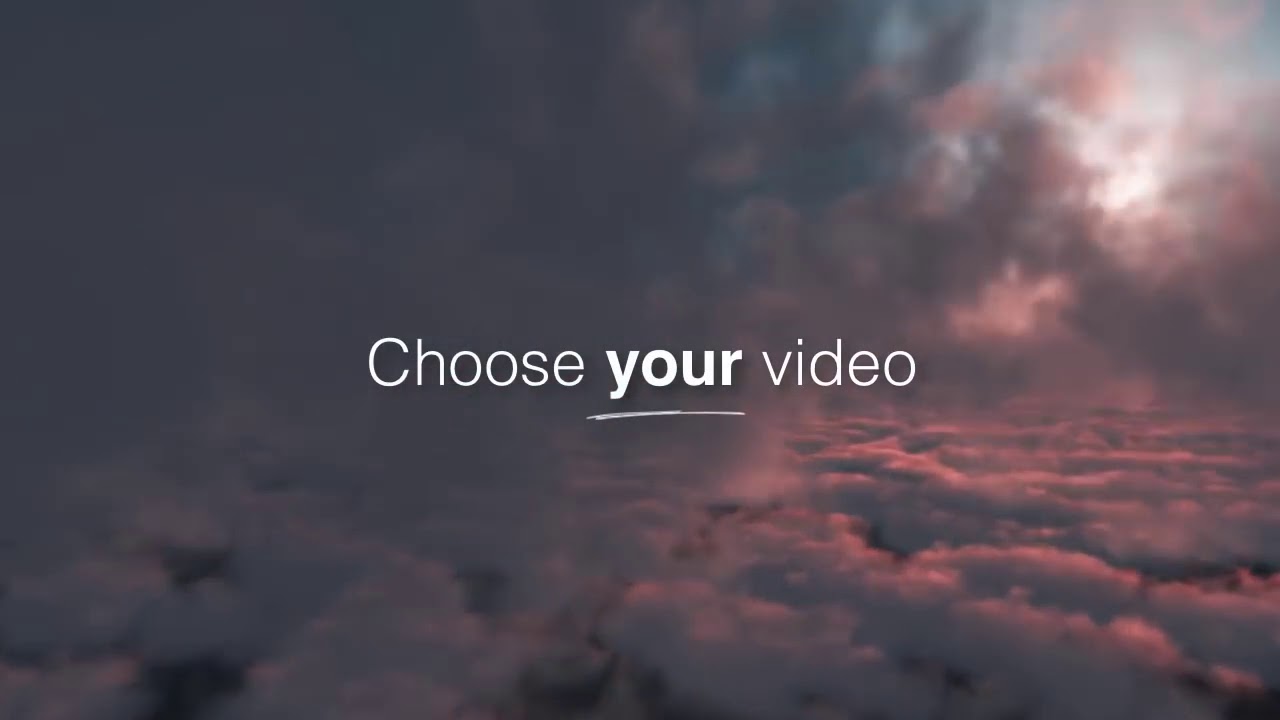
0:16
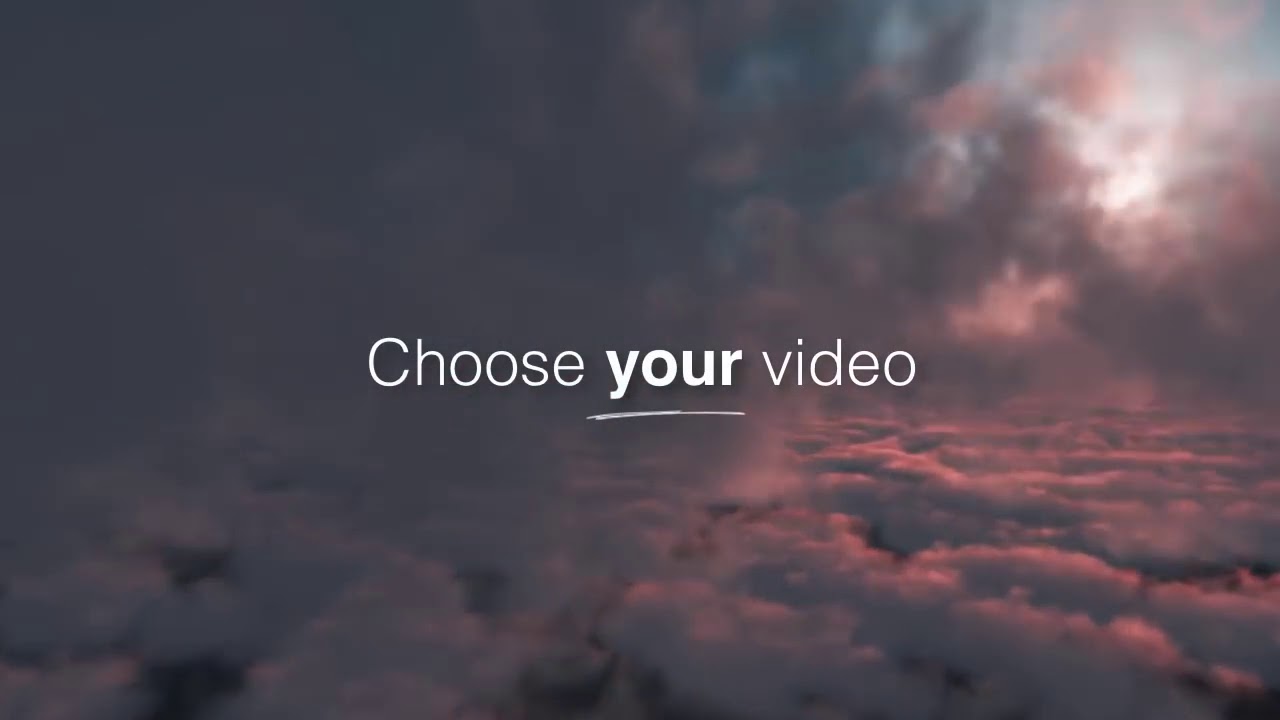